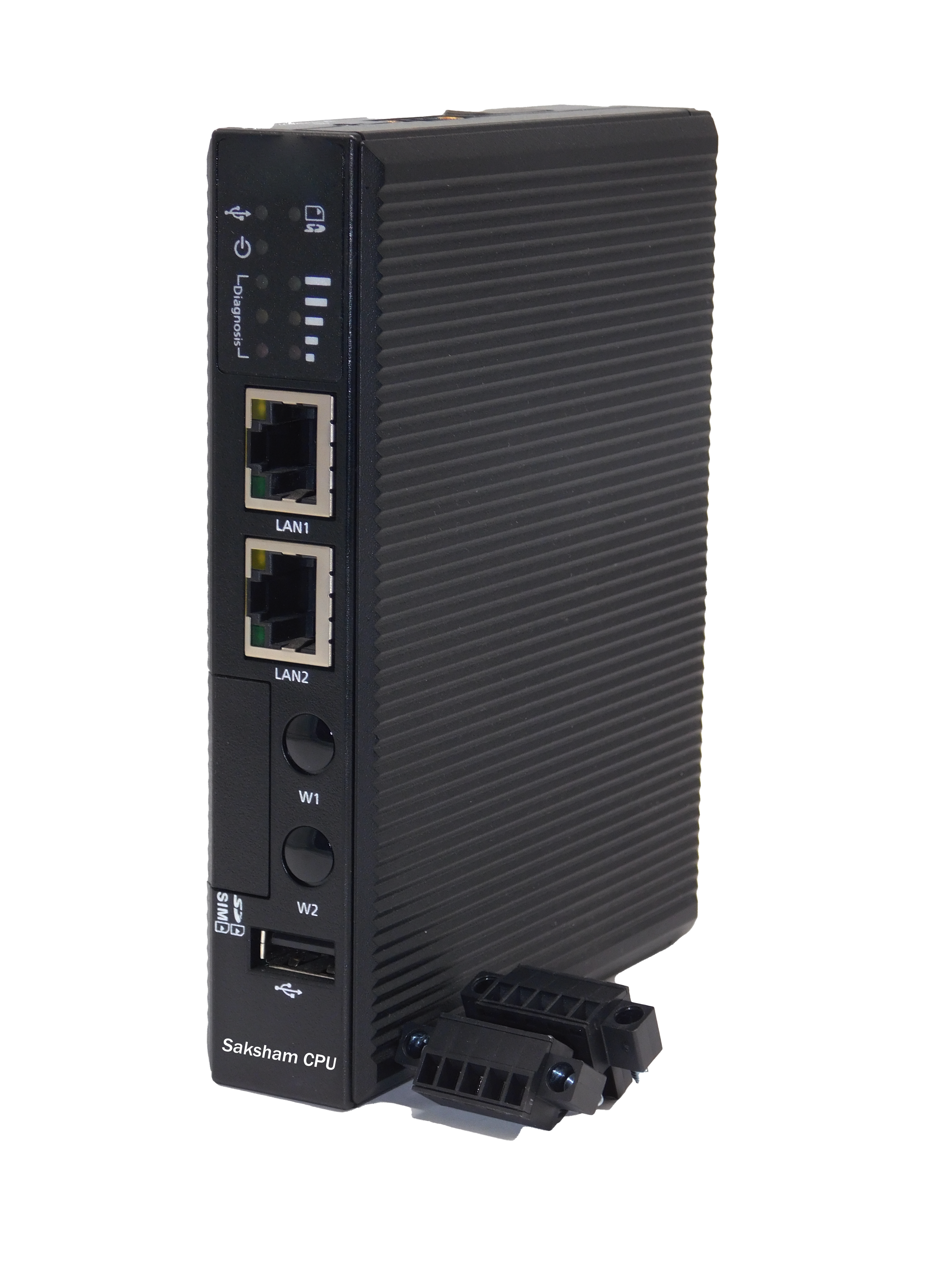
Item No:
Saksham CPU XXXX
DB (Number Range-Maximum Size)
FB (Number Range-Maximum Size)
Fb (Number Range-Maximum size)
OB
Muxmum Size
No Of Free Cycle
No Of Time Alarm
No Of Delay Alarm
No Of Cyclic Interrupt
No Of Process Alarm
No Of DPV1 Alarm
No Of Isochronous Mode
No Of Technology Synchronous Alarm
No Of Startup
No Of Asynchronous Error
No Of Synchronous Error
No Of Diagnostic Alarm
IO Address Area
Inputs
Outputs
Integrated Io Subsystem
Inputs
Outputs
CM/CP
Inputs
Outputs
No. Of IO controller
Integrated
CM
Rack
No. Of module Per Pack
No. of Rack
Clock
Type
Backup Time
Deviation Per Day
Clock Synchronization
Supported
In Mater
In Slave
On Ethernet
Interface Type
Ethernet(RJ-45)
No. Of Ports
Integrated Switch
Protocols
IP Protocols
Modnet Io Controller
Modnet Io Device
Profinet Io Controller
OPC
Web Server
Media Redundency
Profinet Modnet Io Controller Serices
Pg Op Communication
Isocronous Mode
Direct Data Exchange
IRT
Prioritized Startup
No Of Connectable Io Device For Rt
Updating Time
Update Time for IRT
Send Cycle Of 250 πs
Send Cycle Of 500 πs
Send Cycle Of 1 πs
Send Cycle Of 2 πs
Send Cycle Of 4 πs
Update Time for RT
Send Cycle Of 250 πs
Send Cycle Of 500 πs
Send Cycle Of 1 πs
Send Cycle Of 2 πs
Send Cycle Of 4 πs
Profinet Modnet Io Device Services
Pg Op Communication
Isochronous Mode
IRT
Profienergy
Shared Device
Maximum No Of Io Controller With Shared Device
Activation Deactivation Of I Devices
Asset Management Record
RJ-45 Ethernet
100 MBPS
Autonegotiation
Autocrossing
Industrial Ethernet Status Led
No Of Simultaneously Active Program Alarms
No Of Program Alarms
Alarm For System Diagnostic
Alarm For Moton Technology Objects
In the realm of industrial automation the programmable logic controller reigns supreme orchestrating complex machinery and processes with precision and reliability at the heart of every plc lies its central processing unit CPU the veritable brain of the operation the CPU is responsible for executing the user programmed logic interpreting instruction and controlling the PLC's behavior this involves reading input signals from sensors processing data and generating output signals to control actuators and other devices the CPU manages the plc memory storing programs data and system parameters it ensures efficient allocation and access to memory resources optimizing performance and preventing data corruption modern PLCs often feature communication capabilities allowing them to interact with other devices networks and HMI the CPU manages these communication protocols ensuring seamless data exchange and control to maintain system reliability the CPU incorporates self-diagnostic functions it continuously monitor its own operation and that of other plc components detecting potential issues and alerting maintenance personnel the performance and the reliability of a plc are heavily dependent on the capabilities of its CPU a powerful CPU with ample memory and advanced features can handle complex control tasks optimize system performance and enhance overall productivity.
This package includes complete SAKSHAM Engineering Software and SAKSHAM SCADA Runtime Software projects for Saksham PLCs, enabling quick deployment and intuitive control. It comes with detailed documentation for I/O mapping, installation, and troubleshooting. The package also provides TPW-specific libraries and runtime tools to ensure smooth integration and operation.
This Package includes the SAKSHAM Engineering Software Project for Saksham PLCs, ready-to-deploy automation code.The package provides TPW-specific libraries and runtime tools to ensure smooth integration and operation. It also contains detailed documentation covering I/O mapping, installation guides, and troubleshooting support for seamless integration and maintenance.
This Package includes the SAKSHAM SCADA Runtime Software Project with user-friendly visualizations for real-time monitoring and control. It also comes with comprehensive documentation, including screen layouts, configuration steps, and troubleshooting guides for easy setup and smooth operation.
This Package includes a SAKSHAM SCADA Runtime Software Project with intuitive, ready-to-use visualizations for real-time monitoring and control. It ensures seamless integration with Saksham PLCs, offering efficient and user-friendly interface design.
SAKSHAM Library offers a comprehensive set of pre-built code libraries, reusable templates, configuration guides, and integration examples. It simplifies development, accelerates project deployment, and ensures consistency and reliability across Saksham PLC applications.
The SAKSHAM Manual provides complete technical manuals, I/O mapping sheets, installation guides, and troubleshooting checklists. It ensures easy setup, smooth operation, and reliable maintenance support for Saksham PLC systems.